General Provisions
The diameter of CHUANGRONG PE pipes ranges from 20 mm to 1600 mm, and there are many types and styles of fittings available for customers to choose. PE pipes or fittings are joined to each other by heat fusion or with mechanical fittings.
PE pipe also can be joined to other material pipes by means of compression fittings, flanges, or other qualified types of manufactured transition fittings.
Each offer sits particular advantages and limitations for each joining situation the user may encounter. Contact with the various manufacturers is advisable for guidance in proper applications and styles available for joining as described in this document as following.
Connection Methods
There are several types of conventional heat fusion joints currently used in the industry: Butt, Saddle, and Socket Fusion.Additionally, electrofusion (EF) jointing is available with special EF couplers and saddle fittings.
The principle of heat fusion is to heat two surfaces to a designated temperature, then fuse them together by application of a sufficient force. This force causes the melted materials to flow and mix, thereby resulting in fusion. When fused according to the pipe and/or fitting manufacturers' procedures, the joint area becomes as strong as or stronger than, the pipe itself in both tensile and pressure properties and properly fused joints are absolutely leak proof. As soon as the joint cools to near ambient temperature, it is ready for handling.The following sections of this chapter provide ageneral procedural guideline for each of these connection methods.
Butt fusion Steps
1. The pipes must be installed in the welding machine,and the ends cleaned with non depositing alcohol to remove all dirt, dust, moisture, and greasy films from a zone approximately 70 mm from the end of each pipe, on both inside and outside diameter faces.
2.The ends of the pipes are trimmed using a rotating cutter to remove all rough ends and oxidation layers. The trimmed end faces must be square and parallel.
3. The ends of the PE pipes are heated by connection under pressure(P1)against a heater plate. The heater plates must be clean and free from contamination, and maintained within a surface temperature range (210±5 ℃C for PE80, 225±5 C for PE100). Connection is maintained until even heating is established around the pipe ends, and the connection pressure then reduce to a lower value P2(P2=Pd).Connection is then maintained until the "Heat-absorption Step" ends.
Buttfusion
Butt fusion is the most widely used method for joining individual lengths of PE pipes and pipes to PE fittings,which is by heat fusion of the pipe butt ends as illustrated in Figure. This technique produces a permanent,economical and flow-efficient connection. High-quality butt fusion joints are produced by trained operators in good condition.
Butt fusion is generally applied to PE pipes within the size range 63 mm to1600 mm for joints on pipes, fittings and end treatments. Butt fusion provides a homogeneous joint with the same properties as the pipe and fittings materials, and ability to resist longitudinal loads.

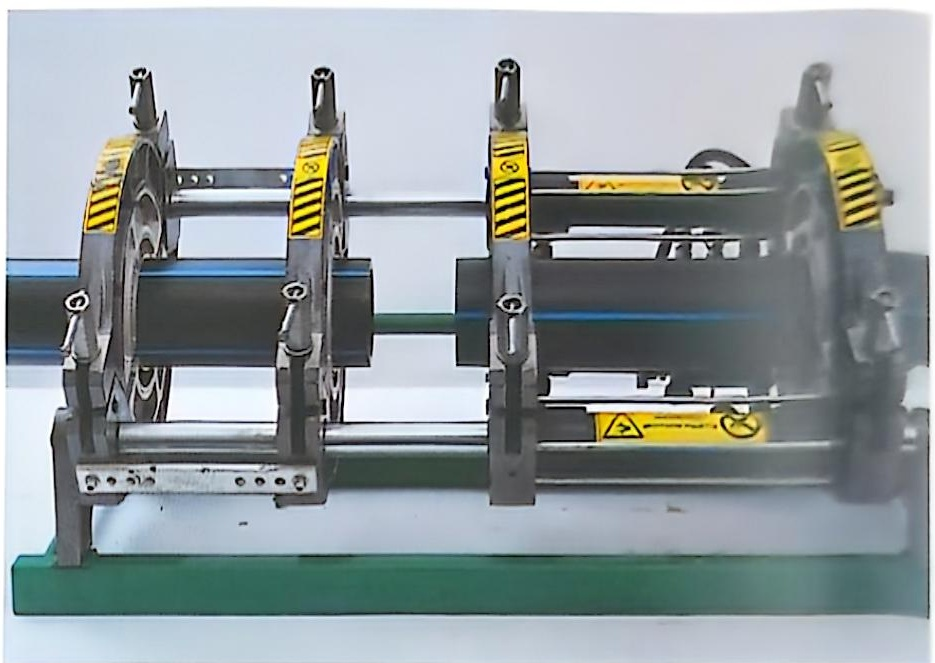
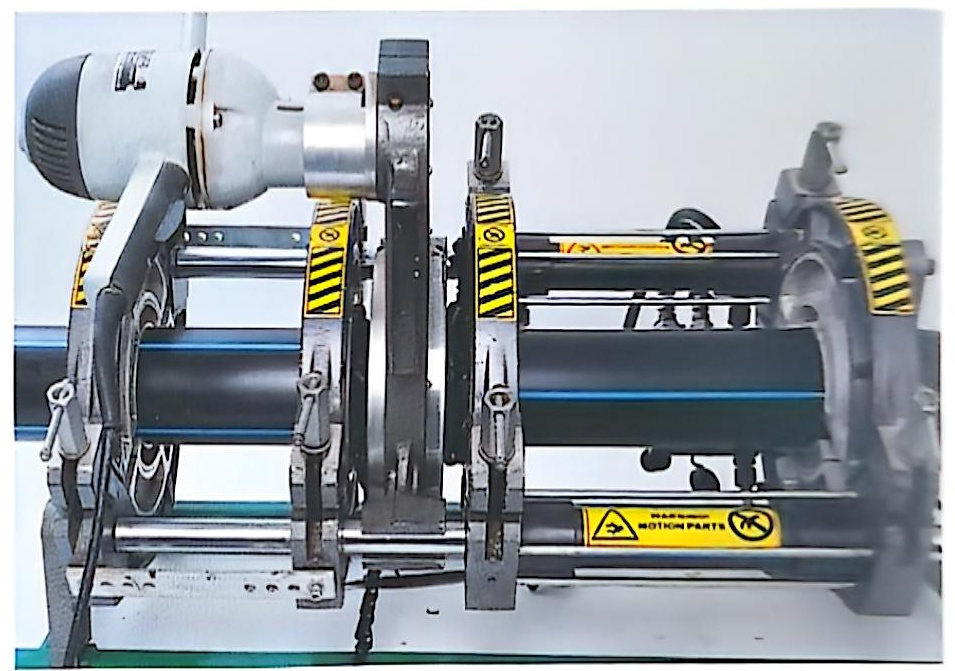
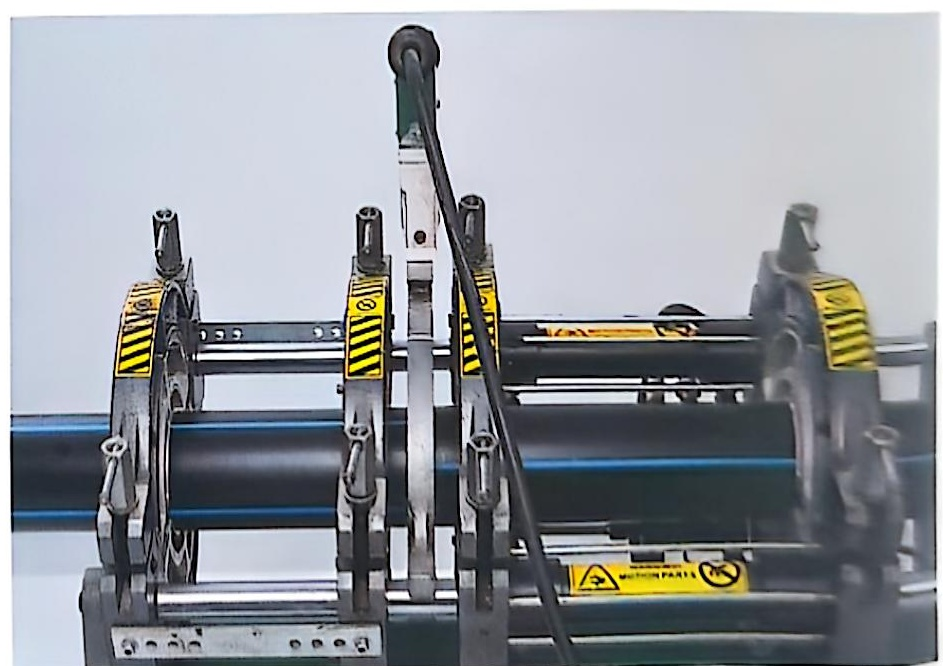
4. The heated pipe ends are then retracted and the heater plate removed as soon as possible (t3: no contact pressure).
5. The heated PE pipe ends are then brought together and pressurized evenly to the welding pressure value(P4=P1).This pressure is then maintained for a period to allow the welding process to take place, and the fused joint to cool down to ambient temperature and hence develop full joint strength.(t4+t5). During this cooling period the joints must remain undisturbed and under compression. Under no circumstances should the joints be sprayed with cold water.The combinations of times, temperatures, and pressures to be adopted depends on the PE material grade,the diameter and wall thickness of the pipes, and the brand and model of fusion machine being used. CHUANGRONG engineers can provide guidance in the separate meters, which are listed in the following forms:
SDR |
SIZE |
Pw |
ew* |
t2 |
t3 |
t4 |
P4 |
t5 |
SDR17 |
(mm) |
(MPa) |
(mm) |
(s) |
(s) |
(s) |
(MPa) |
(min) |
D110*6.6 |
321/S2 1.0 |
66 6 6 321/S2 9 |
||||||
D125*7.4 |
410/S2 |
1.5 |
74 |
6 |
6 |
410/S2 |
12 |
|
D160*9.5 |
673/S2 |
1.5 |
95 |
7 |
7 673/S2 |
13 |
||
D200*11.9 |
1054/S2 |
1.5 |
119 |
8 |
8 |
1054/S2 |
16 |
|
D225*13.4 1335/S2 |
2.0 |
134 |
8 |
8 1335/S2 |
18 |
|||
D250*14.8 |
1640/S2 |
2.0 |
148 |
9 |
9 |
1640/S2 |
19 |
|
D315*18.7 2610/S2 |
2.0 |
187 |
10 |
10 |
2610/S2 24 |
|||
SDR13.6 |
D110*8.1 |
389/S2 |
1.5 |
81 |
6 |
6 |
389/S2 |
11 |
D125*9.2 502/S2 |
1.5 |
92 |
7 |
7 502/S2 |
13 |
|||
D160*11.8 |
824/S2 |
1.5 |
118 |
8 |
8 |
824/S2 |
16 |
|
D200*14.7 1283/S2 |
2.0 |
147 |
9 |
9 |
1283/S2 19 |
|||
D225*16.6 |
1629/S2 |
2.0 |
166 |
9 |
10 |
1629/S2 |
21 |
|
D250*18.4 2007/S2 |
2.0 |
184 |
10 |
11 |
2007/S2 |
23 |
||
D315*23.2 |
3189/S2 |
2.5 |
232 |
11 |
13 |
3189/S2 |
29 |
|
SDR11 |
D110*10 |
471/S2 |
1.5 |
100 |
7 7 |
471/S2 |
14 |
|
D125*11.4 |
610/S2 |
1.5 |
114 |
8 |
8 |
610/S2 |
15 |
|
D160*14.6 1000/S2 |
2.0 |
146 |
9 9 |
1000/S2 |
19 |
|||
D200*18.2 |
1558/S2 |
2.0 |
182 |
10 |
11 |
1558/S2 |
23 |
|
D225*20.5 1975/S2 |
2.5 |
205 |
11 |
12 |
1975/S2 |
26 |
||
D250*22.7 |
2430/S2 |
2.5 |
227 |
11 |
13 |
2430/S2 |
28 |
|
D315*28.6 3858/S2 |
3.0 286 13 15 3858/S2 35 |
ew*is the height of the welding bead at the fusion connection.
The final weld beads should be fully rolled over, free from pitting and voids, correctly sized, and free from discolouration. When correctly performed, the minimum long term strength of the butt fusion joint should be 90%of the strength of the parent PE pipe.
The parameters of the welding connection should conform to the demands in Figure :
B=0.35∼0.45en
H=0.2∼0.25en
h=0.1∼0.2en
Note: Following fusion results should be avoided:
Over-welding: welding rings are too wide .
Unfitness butt fusion: the two pipes are not in alignment.
Dry-welding: welding rings are too narrow,usually due to low temperature or shortage of pressure.
Incomplete curling: welding temperature is too low.
Socket Fusion
For the PE pipes and fittings which have rather small diameters (from 20mm to 63mm), socket fusion is a kind of convenient method. This technique consists of simultaneously heating both the external surface of the pipe end and the internal surface of the socket fitting until the material reaches there commended fusion temperature, inspect the melt pattern, insert the pip end into the socket, and hold it in place until the joint cools.Figure below illustrates atypical socket fusion joint.
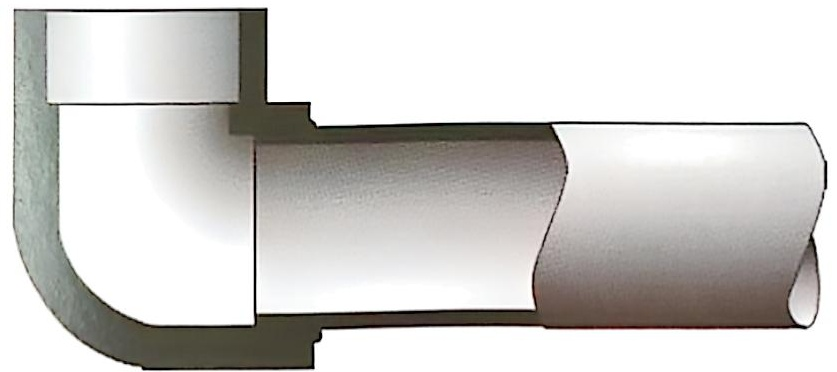
The heater elements are coated by PTFE, and must be kept clean and free from contamination at all times.The heater tools need to be set and calibrated to maintain a stable surface temperature range from 240 Cto 260℃,which depends on the diameter of the pipe. All jointing must be performed under cover to prevent contamination of the joints from dust, dirt,or moisture.
The procedure of socket fusion
1. Cut the pipes, clean the spigot section with a clean cloth and a non depositing alcohol to the full depth of the socket. Mark the length of the socket. Clean the inside of the socket section.
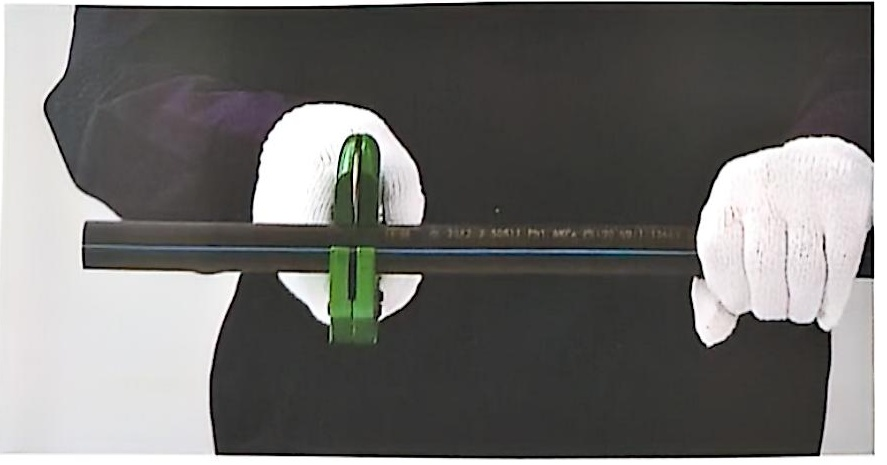
2.Scrape the outside of the pipe spigot to remove the outside layer from the pipe. Do not scrape the inside of the sockets.
3. Confirm the temperature of the heating elements, and ensure that the heating surfaces are clean.
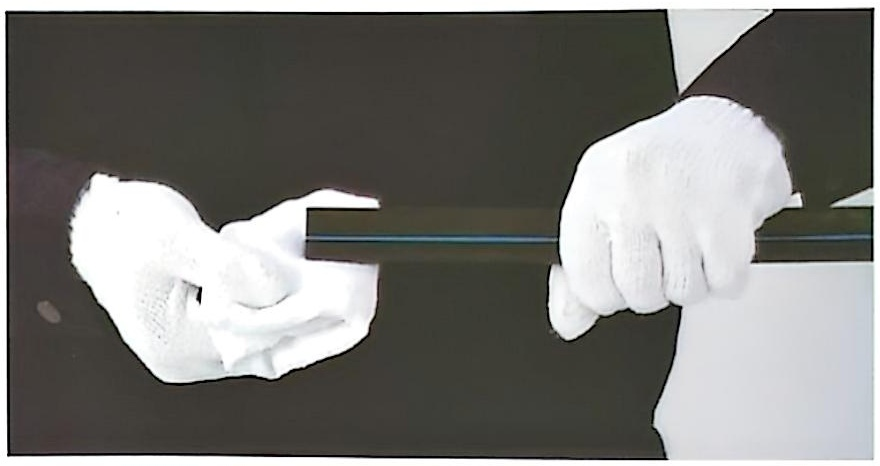
4. Push the spigot and socket sections on to the heating elements to the full length of engagement, and allow to heat for the appropriate period.
5. Pull the spigot and socket sections from the heating elements, and push together evenly to the full length of engagement without distortion of the joints. Clamp the joints and hold until fully cooled. The weld flow bead should then appear evenly around the full circumference of the socket end.
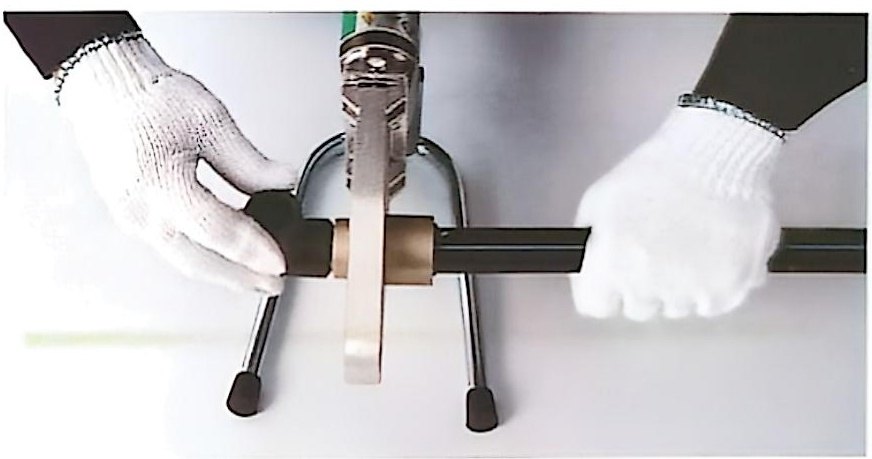
The parameters of socket fusion
dn, mm |
Socket depth, mm |
Fusion temperature, C |
Heating time, S |
Fusion time, S |
Cooling time, S |
20 |
14 |
240 |
5 |
4 |
2 |
25 |
15 |
240 |
7 |
4 |
2 |
32 |
16 |
240 |
8 |
6 |
4 |
40 |
18 |
260 |
12 |
6 |
4 |
50 |
20 |
260 |
18 |
6 |
4 |
63 |
24 |
260 |
24 |
8 |
6 |
75 |
26 |
260 |
30 |
8 |
8 |
90 |
29 |
260 |
40 |
8 |
8 |
110 |
32.5 |
260 |
50 |
10 |
8 |
Note: Socket fusion is not recommended for pipes SDR17 and below.
Mechanical Connections
As in the heat fusion methods, many types of mechanical connection styles and methods are available, such as: flange connection,PE-steel transition part...
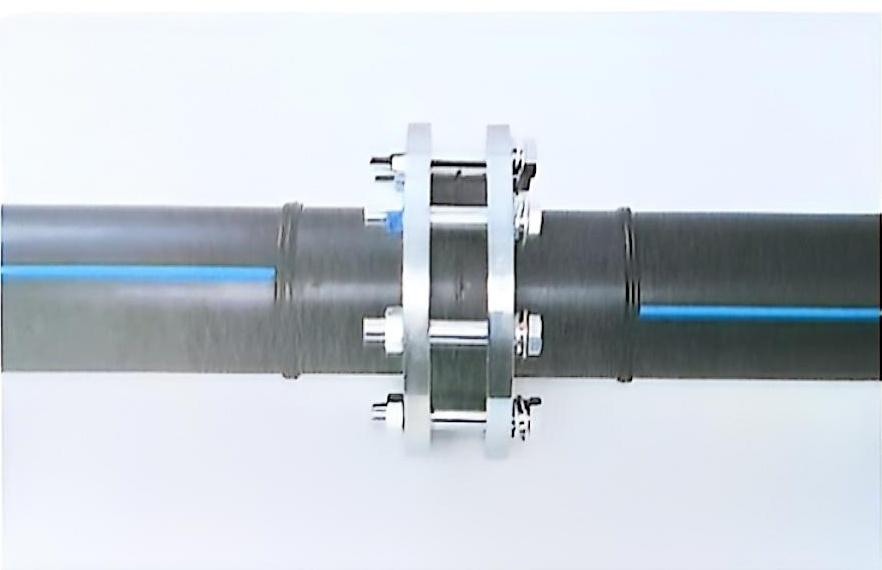
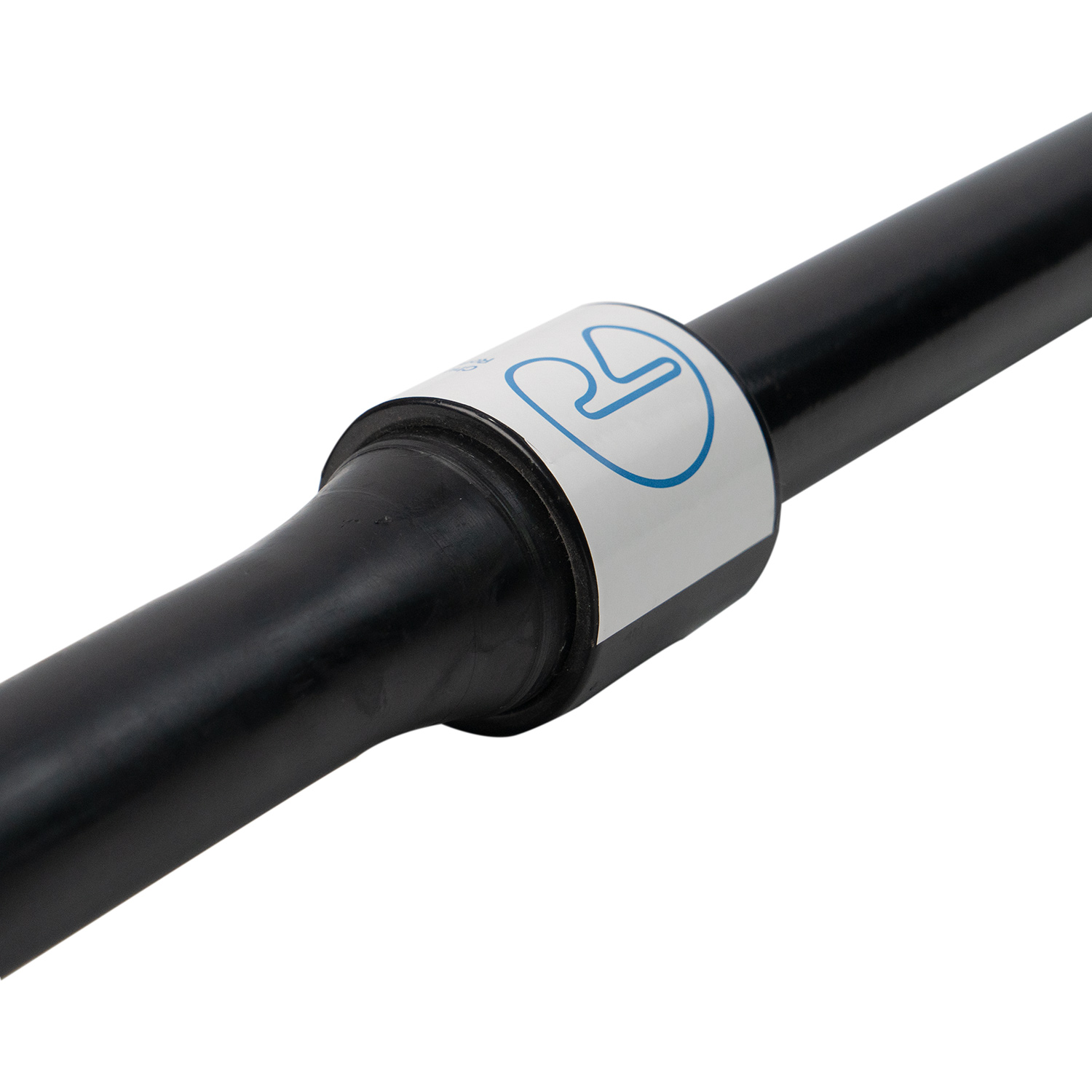
Electrofusion
In conventional heat fusion joining, a heating tool is used to heat the pipe and fitting surfaces. The electrofusion joint is heated internally, either by a conductor at the interface of the joint or, as in one design, by a conductive polymer.Heat is created as an electric current is applied to the conductive material in the fitting. Figure 8.2.3.A illustrates a typical electrofusion joint. PE pipe to pipe connections made using the electrofusion process require the use of electrofusion couplings. The main difference between conventional heat fusion and electrofusion is the method by which the heat is applied.
The procedure of Electrofusion
1. Cut the pipes square, and mark the pipes at a length equal to the socket depth.
2. Scrape the marked section of the pipe spigot to remove all oxidized PE layers to a depth of approximately 0.3mm.Use a hand scraper, or a rotating peel scraper to remove the PE layers. Do not use sand paper. Leave the electrofusion fittings in the sealed plastic bag until needed for assembly. Do not scrape the inside of the fitting,clean with an approved cleaner to remove all dust, dirt, and moisture.
3. Insert the pipe into the coupling up to the witness marks. Ensure pipes are rounded, and when using coiled PE pipes, rerounding clamps may be needed to remove ovality. Clamp the joint assembly.
4. Connect the electrical circuit, and follow the instructions for the particular power control box. Do not change the standard fusion conditions for the particular size and type of fitting.
5. Leave the joint in the clamp assembly until the full cooling time has been completed.
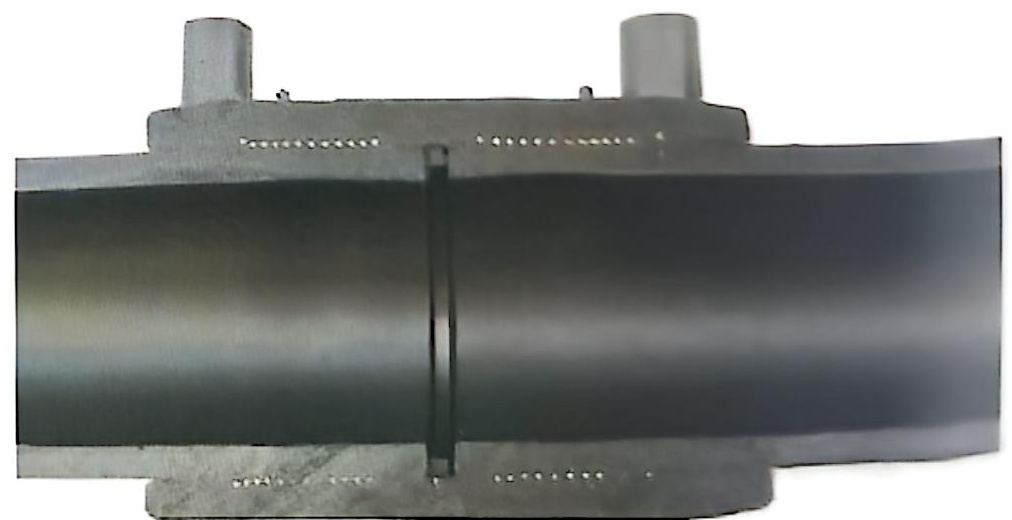
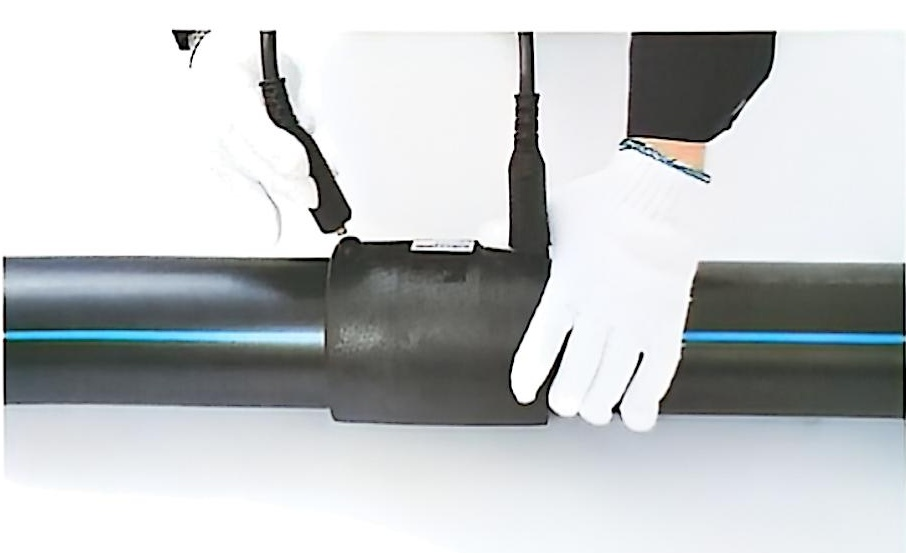
Saddle Fusion
The conventional technique to join a saddle to the side of a pipe,illustrated in Figure8.2.4, consists of simultaneously heating both the external surface of the pipe and the matching surface of the "saddle" type fitting with concave and convex shaped heating tools until both surfaces reach proper fusion temperature. This maybe accomplished by using a saddle fusion machine that has been designed for this purpose.
There are eight basic sequential steps that are normally used to create a saddle fusion joint:
1.Clean the pipe surface area where the saddle fitting is to be located
2. Installthe appropriate size heater saddle adapters
3. Install the saddle fusion machine on the pipe
4. Prepare the surfaces of the pipe and fitting in accordance with the recommended procedures
5.Align the parts
6.Heat both the pipe and the saddle fitting
7.Press and hold the parts together
8. Cool the joint and remove the fusion machine
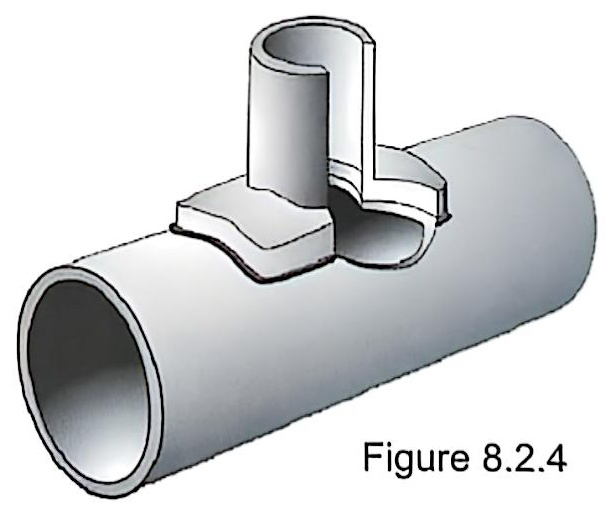
CHUANGRONG is a share industry and trade integrated company, established in 2005 which focused on the production of HDPE Pipes, Fittings & Valves, PPR Pipes, Fittings & Valves, PP compression fittings & Valves, and sale of Plastic Pipe Welding machines, Pipe Tools, Pipe Repair Clamp and so on. If you need more details, please contact us +86-28-84319855, chuangrong@cdchuangrong.com, www.cdchuangrong.com
Post time: Jul-08-2025